Inventor Counterbore Slot
- Inventor Counterbore Slot Kit
- Inventor Counterbore Slot Block
- Inventor Counterbore Slot Tool
- Inventor Counterbore Slot Lock
- Inventor Counterbore Slot Parts
Use the 2D Pocket strategy with a 4 mm flat end tool to machine the counterbore on the single 4.5 mm hole. On the ribbon, click CAM tab 2D Milling panel 2D Pocket. Tool tab For this pocket, a flat tool with a diameter less than 4.5 mm is required to plunge into the pre-drilled hole. On the ribbon Sketch tab Draw panel, click Overall Slot. Click in the graphic window to place the first slot point. Move the cursor, and click to specify slot length. If appropriate, enter the slot length or angle in the edit field. Use the 2D Pocket strategy with a 4 mm flat end tool to machine the counterbore on the single 4.5 mm hole. On the ribbon, click CAM tab 2D Milling panel 2D Pocket. Tool tab For this pocket, a flat tool with a diameter less than 4.5 mm is required to plunge into the pre-drilled hole.
A butt joint is a technique in which two pieces of material are joined by simply placing their ends together without any special shaping. The name 'butt joint' comes from the way the material is joined together. The butt joint is the simplest joint to make since it merely involves cutting the wood to the appropriate length and butting them together. It is also the weakest because unless some form of reinforcement is used (see below) it relies upon glue alone to hold it together. Because the orientation of the wood usually presents only one end to a long grain gluing surface, the resulting joint is inherently weak.[1]
Methods[edit]
The butt joint is a very simple joint to construct. Members are simply docked (cut off) at the right angle and have a required length. One member will be shorter than the finished size by the thickness of the adjacent member. For enclosed constructions, such as four-sided frames or boxes, the thickness of the two adjacent members must be taken into consideration. For example: when constructing a four sided box made from 19mm thick material that is to be of finished size 600mm x 600mm, two of the members will be docked at 600mm and two will be docked at 600mm - 19mm - 19mm = 562mm.
Reinforced butt joints may require additional steps which are detailed below.
In solid timber, docking of members for a butt joint is usually a crosscut, so a crosscut saw is best for this job. When working with sheetgoods, there is no distinction between crosscut and rip cut.
The joint members can be docked by any of the following methods:
- Carcase butt joints
- Circular saw and straightedge
- Frame butt joints
- Crosscut backsaw
- Table saw using a mitre gauge, crosscut sled, or sliding table attachment.
Reinforced butt joints[edit]
To overcome their inherent weakness, butt joints are usually reinforced by one of the following methods:
Nailed butt joint[edit]
This is the most common form of the butt joint in building construction. Members are brought together and a number of nails are driven in to hold them in place. The technique of skew-nailing is applied so that nails are not parallel to each other and so resist the pulling apart of the joint. This form of butt joint is rarely used in furniture making.
Use for:
- framing in building construction, such as platform framing
- Basic or temporary box/cabinet/frame making
- woodwork toys
Dowel reinforced butt joint[edit]
The dowel reinforced butt joint or simply dowel joint has been a very common method of reinforcing butt joints in furniture for years. They are common in both frame and carcase construction. Dowel joints are popular in chairs, cabinets, panels and tabletops. They are also used to assist with alignment during glue up.
The technique consists of cutting the members to size and then drilling a series of holes in the joint surface of each member. Holes are often drilled with the assistance of a dowelling jig which aids in accurate hole placement — accuracy is paramount in this technique to ensure members line up perfectly in the completed joint. The holes are drilled such that there are corresponding holes in each member into which short dowels are inserted with some glue. The joint is brought together and clamped until the glue has dried.
This produces a joint which is much stronger than a butt joint without reinforcement.[2] The dowels offer some holding strength even after the glue has deteriorated. Over time, dowels may shrink and become loose. They take on an oval shape in section owing to the different rate at which wood moves with different orientations of the grain. Loose dowels allow the joint to flex, although it may not fall apart. This phenomenon is evident in creaking chairs and wobbling book cases. For this reason, dowel joints are not preferred for high-quality furniture.Use for:
- Frame joinery (e.g. face frames, web frames, door frames, table legs to aprons, chair legs)
- Cabinet carcase construction (e.g. carcase sides to top and bottom, fixed shelving/partitions)
- Panel assembly (for alignment)
A variation of the dowel method for reinforcement is the use of a Miller dowel in place of the usual straight cylindrical dowel. The Miller dowel is a stepped dowel and is drilled with a special stepped drill bit. It is drilled from the outside face of the frame piece to be joined and therefore generally leaves an exposed dowel protruding after glue dries, and the excess dowell head is thus usually flush cut. The advantages of the special dowel are documented in various media promoting the method, but one advantage that should not be overlooked is speed of assembly. The butt joint can often be joined temporarily and sometimes more accurately with simply glue, allowing faster set up than the usual tedious alignment procedures mentioned above. After the glue dries one or more Miller dowels are then used to reinforce the joint. Dowel trimming and sanding of the surface, followed by normal finishing then proceed in the usual manner. The blind alignment problems of floating dowels are virtually eliminated by the use of the Miller dowel. Not all projects are appropriate for the stepped dowel method if an exposed dowel end is not visually acceptable, however.
Biscuit reinforced butt joint[edit]
The biscuit reinforced butt joint is a fairly recent innovation in butt joint construction. It is used primarily in carcase and frame construction. The biscuit is an oval shaped piece of specially dried and compressed wood, usually beech, which is installed in matching mortises in both members of the joint in a similar fashion to a loose or floating tenon. Biscuit joints are common in both frame and carcase construction. They are particularly convenient for panel glue ups as they facilitate alignment of panel members.
To create the mortise for the biscuit, a biscuit joiner is usually required. There are other methods of cutting the slot, such as a slot cutter bit in a router, but the biscuit joiner is the most common. Accuracy is not as important in the creation of these mortises as the biscuit joint is designed to allow a bit of flexibility during glue up. The mortise must be located at the correct distance from the face of the joint in both members but the width of the mortise is not as critical.
When the mortises have been cut, the biscuit is inserted with some glue and the joint is brought together, aligned and clamped. The biscuit absorbs some moisture from the glue and swells up in the mortise, creating a tightly fitting joint.
Biscuits are available in a range of sizes for different purposes. It is also common to use more than one biscuit side by side in a joint when members are thick.
Use for:
- Frame joinery (e.g. face frames, web frames, table legs to aprons, chair legs)
- Cabinet carcase construction (e.g. carcase sides to top and bottom, fixed shelving/partitions)
- Panel assembly (for alignment)
- Attaching face frames to cabinets
- Bottom
Screwed butt joint[edit]
The screwed butt joint uses one or more screws inserted after the joint has been brought together. The screws are usually inserted into an edge on the long grain side of one member and extend through the joint into the end grain of the adjacent member. For this reason, long screws are required (usually 3 times the thickness of the member) to ensure good traction. These joints may also be glued although it is not necessary.
In solid timber work it is common to counterbore a hole in the frame or carcase member to conceal the head of the screw. This also allows more of the body of the screw to penetrate the adjacent member for greater traction. After the screw has been driven into the joint, the counterbore can be filled with an appropriately sized piece of dowel or a wooden plug cut from an offcut of the same timber using a plug cutter.
There are also commercial systems available for screwed butt joints in which a plastic cap is provided with the screw to be fixed to the head of the screw after it has been driven home. Counterbores are not required for these fasteners. This system is more common with manufactured board products.
The screwed butt joint is common in both frame and carcase joinery. Modular kitchens make regular use of this fixing method.
Use for:
- Frame joinery (e.g. face frames, web frames, door frames)
- Cabinet carcase construction (carcase sides to top and bottom, fixed shelving/partitions)
Inventor Counterbore Slot Kit
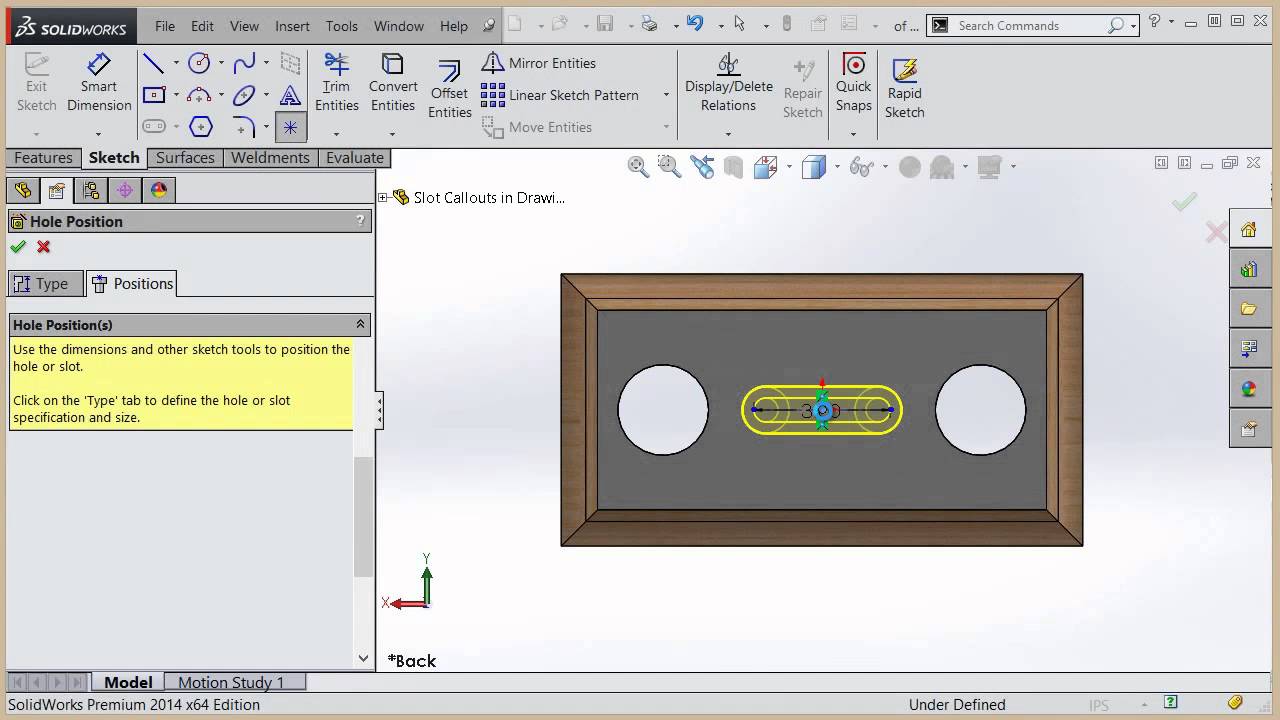
Butt joint with pocket hole screws[edit]
This is a variation of the screwed butt joint in which the screws are inserted into pocket holes drilled in the rear face of one of the joint members. The screws extend into cross grain in the adjacent member, so much shorter screws can be used. This method is preferred when the edges of the frame will be visible.
The pocket holes require two drilling operations to be completed. The first is to counterbore the pocket hole itself, which houses the screw head within the member. This hole is stopped 1/4' (5mm) or so from the edge of the frame member. The second step is to drill a pilot hole concentric with the pocket hole which extends through the edge of the member. The pilot hole allows the screw to pass through the member and into the adjoining member. This two stage drilling operation may be performed with two different sized drill bits, however there are special stepped bits available to perform the operation in a single pass. The drilling operation is often facilitated by a pocket hole jig which allows the user to drill the pocket hole at the correct angle and to the correct depth.
Inventor Counterbore Slot Block
Use for:
- Frame joinery (e.g. face frames, web frames, door frames)
- Attaching face frames to cabinets
Knock-down fasteners[edit]
Knock-down fasteners are a hardware device made for the purpose of constructing butt joints that can be assembled and re-assembled repeatedly (hence knock-down). This type of fastener is very popular in flat-pack furniture, which is typified by items such as book cases and wall units that come in a package of pre-cut and pre-drilled components ready to assemble by a novice. They are also very common in modern modular kitchens.
Knock-down fasteners usually consist of cam dowels locked by cam locks, also known as conformat fasteners, installed in adjacent members. The members are brought together and the joint is secured by turning the cam-lock.
Specialist tools and jigs are often required for the repeatable installation of knock-down fasteners (but not for assembly of prefabricated flat-pack furniture), so they tend to be limited to those who are making mass-produced items. However, there are applications in which the hobbyist can benefit from the range of fasteners that are available. They are easier and require less skill to install than some of the other more traditional techniques.
Knock-down fasteners are typically used for carcase joinery; furniture designs using them are usually of frameless construction.
Used for:
- Wide application in cabinet making depending on type of fastener: particularly in carcase construction (e.g. Carcase sides to top and bottom, fixed shelving/partitions, drawer boxes, counter tops to carcase)
References[edit]
- ^'Woodwork - Butt Joint information and Pictures'. www.woodworkbasics.com. Retrieved 2016-06-16.
- ^'How Strong is a Dowel Joint? - Canadian Woodworking Magazine'. www.canadianwoodworking.com. Retrieved 2018-08-06.
External links[edit]
- Creating Butt Joints - DIY advice on choosing and creating Butt Joints.
GD&T of a counterbored slot
Inventor Counterbore Slot Tool
GD&T of a counterbored slot
Inventor Counterbore Slot Lock
Inventor Counterbore Slot Parts
Relatively new to GD&T. I have a base plate in an assembly with two counterbored slots in it. I know how to geometrically tolerance a normal UN-counterbored slot; i.e;
Link
How do I go about it if the slot is counterbored from the underside to give clearance for a socket head cap screw? Is it the same as dimensioning a counterbored hole minus the diameter symbol? Or should i tolerance the top and counterbored sides seperately?
Any help is much appreciated.
D.